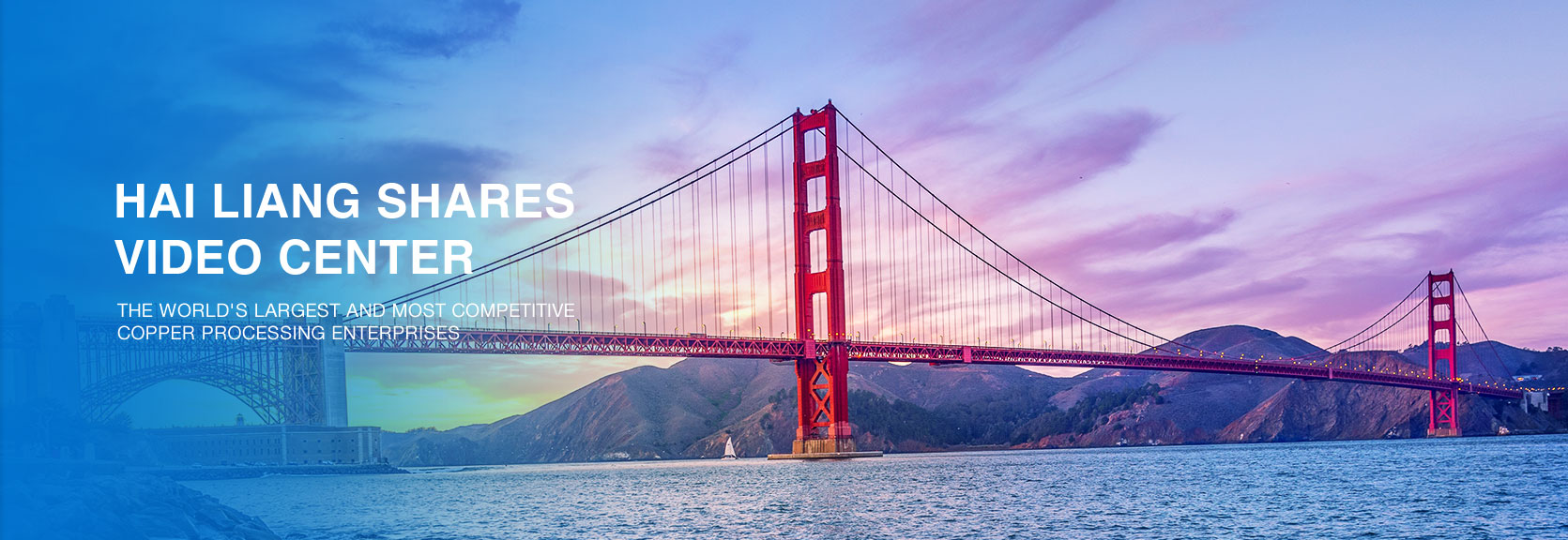
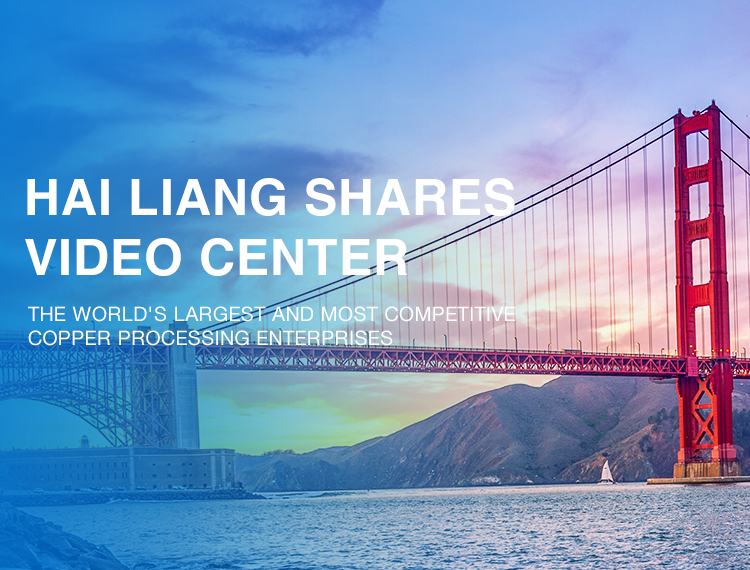
China's transformation from a "large manufacturing country" to a "strong manufacturing country" has a long way to go. China's traditional manufacturing industry has the advantages of large scale, and complete categories as well as system, but the phenomenon of "large more than strong, quantity more than quality" still prevails. How to change through digital transformation has become the "focus" of more and more enterprises.
Zhao Neng, a post-80s generation project engineer of Zhejiang Hailiang Group, and his colleagues have been committed to the digital transformation of the copper processing industry, leading to intelligent reform of traditional manufacturing industries, with practical data to let more people see its value in "lowering costs and increasing efficiency", and strive to develop a digital transformation of their own road.
Opportunities and Challenges Coexist Developing the Digital Transformation Road
Zhao Neng has always believed that digital transformation is the trend, and no one can stop it. The company he worked for before was also a copper processing company, and it was a leading company in the industry. But because the digital transformation was not very successful, his company gradually closed down at a loss. After more than 10 years in the industry, he always has feelings for the industry and knows the need for intelligent and digital development. In 2016, he joined Hailiang Group to engage in the development and management of intelligent production line.
Hailiang Group belongs to the processing and manufacturing industry. Since there was no precedent and no sample to learn from, it was difficult for the group to do intelligent production lines. After studying in the United States and Germany, Zhao Neng found that their methods were even more traditional than those in China. After returning home, he went to Shanghai to visit the robotics exhibition and found that many technologies could be applied to copper processing, so he started from scratch to conceive the planning and architecture needed for digital intelligence reform and set up the intelligent copper processing project.
Zhao Neng recalls that because this was the first digital transformation in the industry, there was a lot of pioneering work and efforts to be made, and the challenges were great for both individuals and companies, but challenges and opportunities coexisted. At that time, all the planning and architecture had to be tried by themselves. They had to keep going through trial and error, and many problems need to be discovered in practice. It is normal to stay at the production site all night. But that is what they want to do, so they make Hailiang a world leading enterprise. Their industrial chain should also be truly leading internationally.
Lowering Costs and Increasing Efficiency Opening up New Elements of Digital Intelligence
At the beginning, it was very difficult to engage in intelligent road, and some old employees were very resistant. In the past, workers were taking paper to copy data and waiting for people to collect orders to count the output. Now employees need to scan the batch number every day to enter the computer system, which makes them very uncomfortable. Zhao Neng said with a smile, at that time people like to give him a thorn in the side, complaining that the equipment does not work well. Later, he taught them one by one, took videos to make visual operation manuals, and told them that digital transformation was the trend and no one could stop it. Those countless trainings made everyone gradually agree and accept such a way.
In the past, the old employees had to do a lot of heavy work in addition to data entry. Copper processing has a very important process called casting slab. A casting slab is 30 meters long and weighs 1.6 tons. Previously, the transfer of casting slabs was done by manpower to tie them, which was a great safety hazard. After Zhao Neng found out, he designed a digital intelligent device. Now, with only one employee on the operating table to click on the button, the huge casting slab will be immediately transferred automatically. Many senior personnel joke that they can't work anymore when they are a little older according to the traditional way, but now they can definitely work until retirement. These intelligent devices make the manpower easier and the safety hazards are gone.
Besides, there are more than 3,000 data collection points totally in the factory, generating more than 200,000 data every day, and its data volume is huge. If stored to their own servers, they have to be overwritten every once in a while, and the data that they want to check six months ago is no longer available. Zhao Neng's team cooperated with Huawei Cloud and solved the problem of efficient data aggregation through ROMA solution.
And now, production can be fully visualized through curves and data to optimize production deployment strategies in real time. In addition, Huawei Cloud also ensures the integrity and security of data storage, utilizing the out-of-the-box feature of security and database services on the cloud to complete the opening of resources and business deployment at the minute level, with a comprehensive cost reduction of 30% in IT resources and more agile business efficiency. After the system is on the cloud, the security architecture is upgraded simultaneously, and the business reliability is increased by 50% through the construction of disaster recovery and security equal protection.
In fact, the changes brought by digital transformation are not only here. Zhao Neng said that Huawei Cloud helped Hailiang Group's whole business to the cloud and data governance, which opened a new journey of digitalization belonging to Hailiang. Our digital factory opens up the whole business process and achieves an increase in the rate of finished products from 91% to 93%; the integrated energy consumption per unit of product drops by 300kwh and the labor efficiency increases by 3 times.
Let Young People also "can" Take over the Traditional Manufacturing Industry
In addition, the traditional manufacturing production furnace has a poor working environment, so many young people would rather deliver take-out than do this. While the production furnace is the most important step in the process of deciding the quality of products, and its requirements for staff experience should be great. But now through data analysis and collation, this step of the process in the future will not need to rely on experience, which just depend on the data. This has greatly improved the threshold and working environment for young people.
In Zhao Neng's view, the problem encountered by enterprises today is that it is difficult to recruit workers because the working environment of manufacturing industry is poorer, unlike other industries where work can be done by sitting in an office. So, the intelligent equipment manufactured can make more young people willing to join the manufacturing industry.
If there are no young people involved in the manufacturing industry, when the teachers are retired, there will be a break in the generation. Intelligent can make many young people come to the manufacturing industry and make the manufacturing industry better and better. Now the leaders of the workshop in the company are very young, basically not more than thirty years old. They are students at elite universities who can get to grips with data quickly and get to work quickly. Zhao Neng also has a deep-seated idea that he wants his children to enter the intelligent manufacturing industry in the future. At ordinary times, he will tell them a lot of interesting things about the industry.
"Manufacturing is actually very interesting, especially after the intelligent transformation. If more and more young people are willing to join our industry, we won't be like Europe and break the generation." Zhao Neng said, "Digital transformation is the trend, and no one can stop it. We need to develop more intelligent production lines and open up new elements of digital intelligence. Let more young people can pay attention to this industry, so that they also 'can' take over the traditional manufacturing industry, pass the technology from generation to generation, and develop this industry better!"